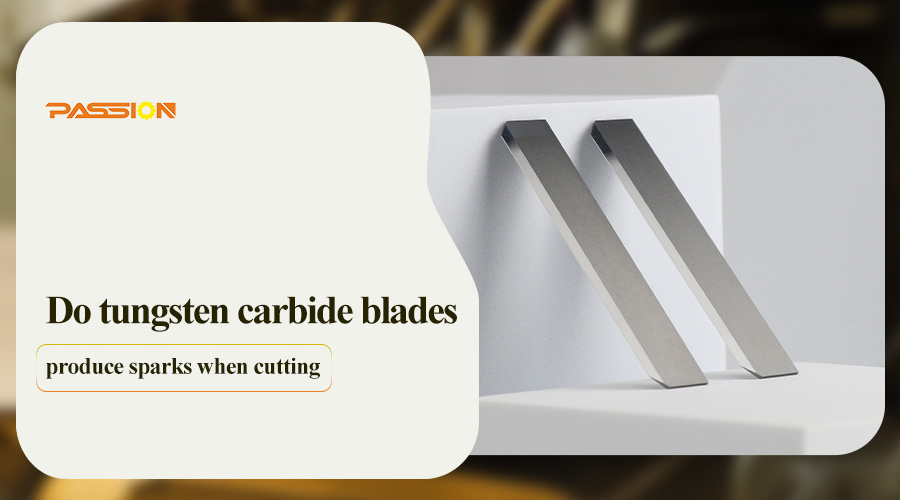
في مجال التصنيع الصناعي ،شفرة كربيد التنغستنأصبح الرائد في قطع العمليات بسبب قوتها العالية والصلابة العالية ومقاومة التآكل الممتازة. ومع ذلك ، بشكل عام ، عندما تدور الشفرات الصناعية بسرعات عالية أثناء عملية القطع وتتلامس وثيقًا للمواد المعدنية ، تحدث ظاهرة جذابة للنظر بهدوء - يطير الشرر. هذه الظاهرة ليست مثيرة للاهتمام فحسب ، بل تثير أيضًا أسئلة حول ما إذا كانت شفرات كربيد التنغستن تنتج دائمًا الشرر عند القطع. في هذه المقالة ، سوف نستكشف هذا الموضوع بعمق ونقدم على وجه التحديد أسباب عدم إنتاج شفرات كربيد التنغستن الشرر عند القطع في ظل ظروف معينة.
شفرة كربيد التنغستن، كنوع من كربيد الأسمنت ، يتكون بشكل أساسي من التنغستن والكوبالت والكربون والعناصر الأخرى ، والتي تمنحها خصائص مادية وكيميائية ممتازة. في عمليات القطع ، تكون شفرات كربيد التنغستن قادرة على قطع المواد المعدنية المختلفة بسهولة مع حوافها الحادة وتناوبها عالي السرعة. ومع ذلك ، في ظل ظروف منتظمة ، عندما تدور الشفرة بسرعة عالية لقطع المعدن ، سيتم إشعال جزيئات صغيرة على سطح المعدن بسبب ارتفاع درجة الحرارة الناتجة عن الاحتكاك ، وتشكيل الشرر.
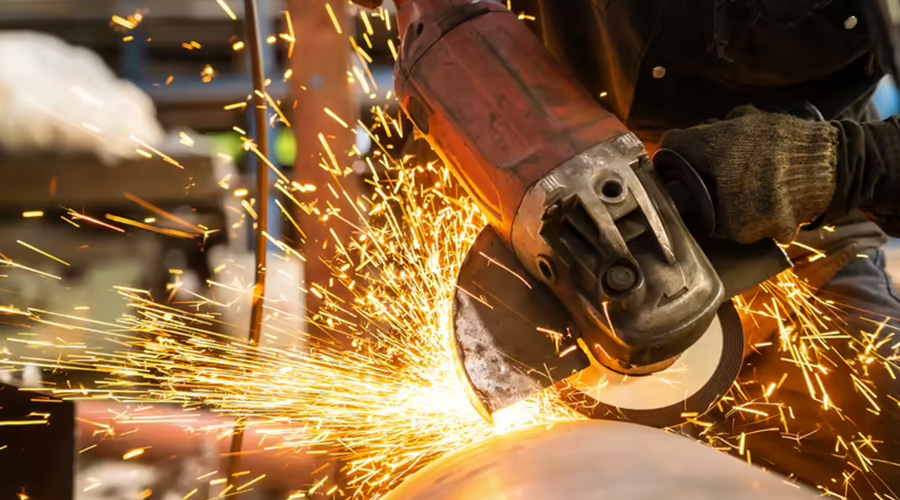
ومع ذلك ، لا تنتج جميع شفرات كربيد التنغستن الشرر عند القطع. في ظل ظروف معينة محددة ، مثل استخدام نسب خاصة لمواد كربيد التنغستن أو اعتماد عمليات قطع محددة ، يمكن أن تقطع شفرات كربيد التنغستن دون الشرر. وراء هذه الظاهرة تكمن المبادئ الفيزيائية والكيميائية المعقدة.
بادئ ذي بدء ، فإن النسبة الخاصة للمواد الصلب التنغستن هي المفتاح. عند تصنيع شفرات كربيد التنغستن ، يمكن تغيير البنية المجهرية والتكوين الكيميائي للشفرة عن طريق ضبط محتوى ونسبة التنغستن والكوبالت والكربون وغيرها من العناصر. تؤدي هذه التغييرات إلى شفرات لها معامل أقل من الاحتكاك والتوصيل الحراري الأعلى أثناء عملية القطع. عندما تكون الشفرة على اتصال مع المعدن ، يمكن امتصاص الحرارة الناتجة بسبب الاحتكاك بسرعة بواسطة الشفرة وإجراءها ، وتجنب إشعال الجسيمات الصغيرة على سطح المعدن ، مما يقلل من توليد الشرارات.
ثانياً ، يعد اختيار عملية القطع أمرًا بالغ الأهمية. في عملية القطع ، يمكن التحكم في الاحتكاك ودرجة الحرارة بين الشفرة والمعادن عن طريق ضبط المعلمات مثل سرعة القطع وعمق القطع وزاوية القطع. عندما تكون سرعة القطع معتدلة ، يكون عمق القطع ضحلًا وزاوية القطع معقولة ، يمكن تقليل الاحتكاك ودرجة الحرارة بشكل كبير ، مما يقلل من توليد الشرر. بالإضافة إلى ذلك ، يمكن أن يؤدي استخدام سائل التبريد لتبريد وتشحيم مساحة القطع أيضًا إلى تقليل درجة حرارة سطح المعدن بشكل فعال ويقلل من الاحتكاك ، مما يقلل من توليد الشرر.
بالإضافة إلى الأسباب المذكورة أعلاه ، قد يكون الافتقار إلى الشرر عند القطع بشفرات كربيد التنغستن مرتبطة أيضًا بطبيعة المادة المعدنية. تحتوي بعض المواد المعدنية على نقطة انصهار منخفضة ومقاومة عالية للأكسدة ، والتي ليس من السهل إشعالها في عملية القطع. عندما تتلامس هذه المعادن مع شفرات كربيد التنغستن ، يكون من الصعب تشكيل الشرر حتى لو تم إنشاء كمية معينة من الاحتكاك ودرجة الحرارة.
ومع ذلك ، تجدر الإشارة إلى أنه على الرغم من أن مواد الصلب التنغستن المتناسب بشكل خاص وعمليات القطع المحددة يمكن أن تقلل من توليد الشرر إلى حد ما ، إلا أنها لا تستطيع التخلص تمامًا من الشرر. في التطبيقات العملية ، لا يزال من الضروري اتخاذ تدابير السلامة اللازمة ، مثل ارتداء نظارات واقية وملابس وقفازات مقاومة للحريق ، لضمان سلامة المشغلين.
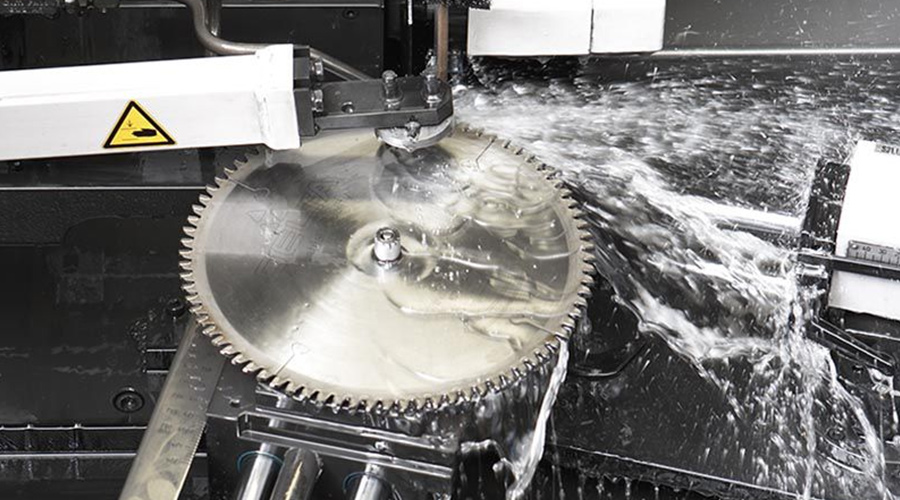
بالإضافة إلى ذلك ، بالنسبة للحالات التي يجب فيها تنفيذ عمليات القطع في بيئات قابلة للاشتعال ومتفجرة ، يجب اختيار المعدات والشفرات مع الأداء المقاوم للانفجار لتقليل خطر الحريق والانفجار. في الوقت نفسه ، يعد الفحص المنتظم وصيانة معدات القطع والشفرات لضمان أن تكون في حالة عمل جيدة أيضًا مقياسًا مهمًا لتقليل توليد الشرارة.
لتلخيص ، سواءشفرة كربيد التنغستنسوف يولد الشرر عند القطع يعتمد على مجموعة من العوامل. من خلال ضبط نسبة مواد الصلب التنغستن ، وتحسين عملية القطع واختيار المواد المعدنية الصحيحة وغيرها من التدابير ، يمكن تقليل توليد الشرارة إلى حد ما. ومع ذلك ، لا يزال من الضروري اتخاذ تدابير حماية السلامة اللازمة وتدابير التفتيش والصيانة المنتظمة في التطبيق العملي لضمان سلامة وكفاءة عمليات القطع. مع التقدم المستمر في العلوم والتكنولوجيا والتحسين المستمر لعملية التصنيع ، يُعتقد أنه في المستقبل ستكون هناك تقنيات ومقاييس أكثر ابتكارًا لتقليل توليد الشرر وتعزيز السلامة والتنمية المستدامة لمجال التصنيع الصناعي.
في وقت لاحق ، سوف نستمر في تحديث المعلومات ، ويمكنك العثور على مزيد من المعلومات على مدونة موقعنا (PassionTool.com).
بالطبع ، يمكنك أيضًا الانتباه إلى وسائل التواصل الاجتماعي الرسمية لدينا:
وقت النشر: ديسمبر -27-2024